فهرست عناوین
نوشته شده توسط شرکت صنایع متانول ایران
منتشر شده توسط شرکت صنایع متانول ایران
تاریخ انتشار مقاله : 27-02-1404
تاریخ بروزرسانی مقاله : 27-02-1404
تعداد کلمات : 2700
آدرس مقاله : لینک مقاله
تولید متانول از ذغال سنگ و هیدروکربن های سنگین
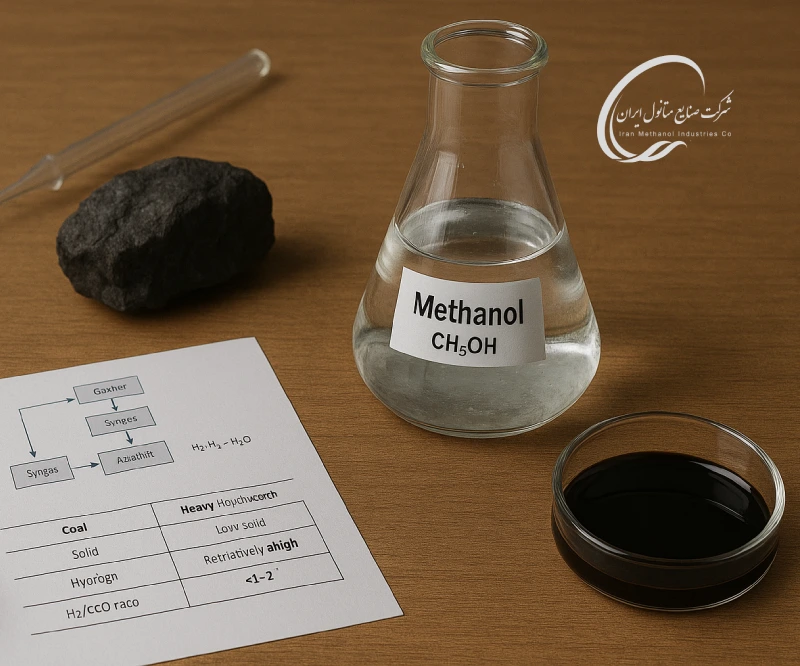
مقدمه
متانول یک الکل ساده با فرمول شیمیایی CH3OH است. این ماده یک حلال صنعتی مهم و خوراک اولیه برای تولید بسیاری از مواد شیمیایی مانند فرمالدهید و اسید استیک محسوب می شود. علاوه بر این، متانول به عنوان یک سوخت جایگزین نیز مورد توجه قرار گرفته است و می توان آن را به صورت خالص یا در ترکیب با بنزین (مثلاً سوخت M85) در موتورهای احتراق داخلی استفاده کرد. امروزه متانول صنعتی عمدتاً از گاز طبیعی (از طریق ریفورمینگ بخار) یا از ذغال سنگ از طریق فرآیند گازسازی تولید می شود. در برخی کشورها که گاز طبیعی محدود است اما ذغال سنگ فراوانی دارند، از فناوری «ذغال سنگ به متانول» (CTM) استفاده می شود. برای مثال، چین به تنهایی نزدیک به ۶۰٪ تولید متانول جهان را به خود اختصاص داده و بیش از ۸۰٪ متانول تولیدی این کشور از ذغال سنگ حاصل می شود. همچنین پسماندهای سنگین هیدروکربنی مانند نفت کوره و کک نفتی نیز از خوراک های قابل استفاده برای تولید متانول هستند که از طریق گازسازی به گاز سنتز تبدیل می شوند. در ادامه، فرآیند تبدیل ذغال سنگ و هیدروکربن های سنگین به متانول را به زبانی علمی اما قابل فهم برای عموم بررسی میکنیم.
ذغال سنگ و هیدروکربن های سنگین: منابع تولید متانول
ذغال سنگ یک سوخت فسیلی جامد با محتوای کربن بالا است که در کشورهایی مانند چین به عنوان ماده اولیه برای تولید متانول صنعتی استفاده می شود. برتری ذغال سنگ در دسترس بودن گسترده و قیمت نسبتاً پایین آن است، هرچند محتوای گوگرد و خاکستر آن نیازمند مدیریت است. از سوی دیگر، هیدروکربن های سنگین مانند نفت سنگین، نفت کوره (مازوت) و کک نفتی نیز می توانند به عنوان خوراک جهت تولید متانول به کار روند. این مواد پسماندهای سنگینی هستند که در پالایشگاهها یا صنایع پتروشیمی به وفور یافت می شوند و دارای کربن زیاد و ارزش حرارتی بالایی هستند. با توسعه فناوری گازسازی، امکان تبدیل این هیدروکربن های سنگین به گاز سنتز فراهم شده است؛ به طوری که فناوری گازسازی نفت سنگین و حتی کک نفتی توسط شرکتهایی نظیر شل و تکزاکو طی حدود ۴۰ سال گذشته به مرحله تجاری رسیده است. استفاده از خوراک های سنگین نه تنها از منظر تأمین خوراک متانول در مناطق فاقد گاز طبیعی مهم است، بلکه روشی برای بهرهبرداری از پسماندهای نفتی کمارزش و تبدیل آنها به محصولات شیمیایی باارزش مانند متانول محسوب می شود.
فرآیند گازسازی: تبدیل سوخت جامد و مایع به گاز سنتز
شکل: دیاگرام بلوکی ساده فرآیند تولید متانول از ذغال سنگ. در این نمودار، ذغال سنگ ابتدا وارد واحد گازسازی شده و در حضور اکسیژن خالص (تأمینشده از واحد تفکیک هوا) و بخار آب به گاز سنتز تبدیل می شود. سپس گاز سنتز ناخالص خنک شده و با عبور از واحد شیفت (جهت افزایش هیدروژن) و واحد تصفیه گاز های اسیدی (جهت حذف گوگرد و CO2) به ترکیب مناسب برای سنتز متانول می رسد. در مرحله بعد، گاز سنتز تمیز و فشردهشده وارد راکتور سنتز متانول شده و متانول خام تولید می شود. متانول خام نیز در واحدهای تفکیک و تقطیر، خالصسازی شده و به عنوان محصول نهایی (متانول صنعتی) ذخیره می گردد.
فرآیند گازسازی (Gasification) با حرارتدهی سوخت در حضور مقدار کنترلشدهای از اکسیدکننده (معمولاً اکسیژن یا هوا) و عامل بخار انجام می شود. در این فرآیند، بخشی از کربن سوخت می سوزد و حرارت آزادشده موجب انجام واکنشهایی مانند واکنش کربن با بخار آب می شود:محصول اصلی گازسازی، گاز سنتز شامل مونوکسید کربن (CO) و هیدروژن (H2) است. دمای عملیات معمولاً بسیار بالا (در حدود ۱۰۰۰ تا ۱۵۰۰ درجه سانتیگراد) بوده و فشار نیز بسته به طراحی می تواند بالا باشد (دهها اتمسفر). در مورد ذغال سنگ، خاکستر معدنی موجود در سوخت ذوب شده و به صورت سرباره جامد از پایین گازساز خارج می شود؛ برای نفت سنگین نیز معمولاً مقدار کمی کک یا سرباره فلزی تشکیل می شود که قابل دفع یا پردازش است. ترکیب گاز سنتز حاصل به ماهیت خوراک وابسته است؛ ذغال سنگ به دلیل هیدروژن کمتر در ساختار خود نسبت H2 به CO پایینتری در گاز سنتز تولیدی دارد، در حالی که هیدروکربن های سنگین به علت محتوای هیدروژن بالاتر، گاز غنیتری از هیدروژن تولید می کنند. جدول زیر مقایسهای کلی میان ذغال سنگ و یک هیدروکربن سنگین (نفت کوره یا کک نفتی) به عنوان خوراک گازسازی ارائه میدهد:
ویژگی | ذغال سنگ | هیدروکربن سنگین (مثلاً نفت کوره) |
---|---|---|
حالت فیزیکی | جامد | مایع یا نیمه جامد |
محتوای هیدروژن (در سوخت) | کم (چند درصد) | بیشتر (چندین برابر ذغال سنگ) |
ناخالصیها (عناصر مزاحم) | خاکستر معدنی، گوگرد | گوگرد بالا، فلزات سنگین |
محصولات جامد فرعی در گازسازی | خاکستر و سرباره زیاد | سرباره یا کک اندک |
نسبت H2 به CO در گاز سنتز خام | پایین (~0.5–1) نیازمند تنظیم | بالاتر (~1–2) مناسبتر |
همانطور که دیده می شود، ذغال سنگ به علت هیدروژن کمتر، گاز سنتزی با نسبت H2/CO پایین تولید می کند که برای سنتز متانول نیاز به اصلاح دارد، در حالی که گاز سنتز حاصل از یک خوراک هیدروکربنی سنگین از نظر مجموع هیدروژن و مونوکسید کربن غنیتر است.
پالایش و آمادهسازی گاز سنتز
گاز سنتز خام خروجی از گازساز حاوی آلایندهها و گاز های نامطلوبی است که قبل از ورود به واحد سنتز متانول باید حذف شوند. از جمله این ناخالصیها می توان به ذرات جامد (خاکستر و دوده)، ترکیبات گوگردی (H2S و COS حاصل از گوگرد سوخت) و گاز های اسیدی مانند CO2 اشاره کرد. اولین گام، خنک کردن گاز داغ و جداسازی ذرات و قطرات قیر (در صورت وجود) توسط شویندهها و فیلترها است. سپس برای افزایش نسبت هیدروژن به مونوکسید کربن، قسمتی از CO موجود در گاز سنتز در راکتور «شیفت گاز-آب» با واکنش با بخار به H2 تبدیل می شود (CO + H2O → H2 + CO2). این واکنش نسبت H2/CO را به مقدار مطلوب (~۲) برای سنتز متانول می رساند. به عنوان مثال، گاز سنتز حاصل از گازسازی ذغال سنگ معمولاً نسبت H2/CO در حدود 0.3 تا 1 دارد که با اجرای واکنش شیفت، هیدروژن آن افزایش یافته و نسبت به حدود 2 نزدیک می شود. در گام بعدی، گاز سنتز از واحد حذف گاز های اسیدی عبور می کند؛ در این واحد با استفاده از حلالهای شیمیایی (مانند آمینها) گاز CO2 و H2S از جریان گاز جدا می شوند. حذف ترکیبات گوگردی بسیار ضروری است زیرا حتی مقادیر جزئی سولفید هیدروژن می تواند کاتالیزور سنتز متانول را مسموم کند. گوگرد بازیابیشده معمولاً به صورت محصول جانبی (گوگرد عنصری یا اسید سولفوریک) استخراج می شود. گاز CO2 جداشده نیز عمدتاً به جو تخلیه می گردد (در صورت وجود زیرساخت، می توان آن را برای دفع دائم یا استفاده ثانویه فشرده و ذخیره کرد). پس از این مراحل، گازی که اصطلاحاً «گاز سنتز تمیز» نامیده می شود به نسبتهای مناسب H2 و CO (حدود 2 به 1) و عاری از ناخالصیهای مضر رسیده است. چنین گاز سنتز پاکی – چه از ذغال سنگ تأمین شده باشد و چه از یک نفت سنگین – آماده ورود به واحد سنتز متانول است و می تواند برای تولید انواع محصولات شیمیایی مانند متانول مورد استفاده قرار گیرد.
تبدیل گاز سنتز به متانول
کاتالیزور و شرایط واکنش
پس از آمادهسازی گاز سنتز، مرحله اصلی تبدیل آن به متانول در راکتور سنتز انجام می شود. واکنش اصلی، ترکیب مونوکسید کربن و هیدروژن است:همچنین در صورتی که گاز سنتز حاوی CO2 باشد، واکنش زیر نیز رخ میدهد:هر دو واکنش شدیداً گرماده (اگزوترمیک) هستند. سنتز متانول به صورت صنعتی با استفاده از کاتالیزورهای ناهمگن انجام می شود؛ کاتالیزور رایج ترکیبی از مس، اکسید روی و آلومینا (Cu/ZnO/Al2O3) است که در دمای حدود ۲۰۰ الی ۳۰۰ درجه سانتیگراد و فشار نسبتاً بالا (مثلاً ۵۰–۱۰۰ اتمسفر) بهینه عمل میکند. شرایط عملیاتی دقیق بسته به طراحی فرآیند و تأمینکننده کاتالیزور متفاوت است، اما به طور کلی برای دستیابی به نرخ تبدیل مناسب، فشار بالا و دمای متوسط به همراه بازیافت مداوم گاز های واکنشنیافته به کار گرفته می شود.
فرآیند سنتز متانول معمولاً در راکتورهای بستر ثابت انجام میگیرد که در آن گاز سنتز پس از فشردهسازی وارد بستر کاتالیزوری شده و طی عبور از آن، بخشی از CO و CO2 به متانول تبدیل می شوند. به علت محدودیت تعادلی واکنش، میزان تبدیل در هر پاس کامل نیست (مثلاً تنها بخشی از گاز واکنش مییابد)؛ بنابراین طراحی واحدهای متانول به صورت حلقه گردش انجام شده که گاز خروجی غیرواکنشیافته (عمدتاً هیدروژن) را دوباره به ورودی راکتور برمیگرداند. متانول تولیدشده به صورت بخار همراه با گاز های خروجی از راکتور خارج می شود که با سرد کردن این جریان، متانول مایع به صورت محصول خام جدا می گردد. متانول خام معمولاً حاوی آب و مقادیر جزیی از محصولات فرعی (مانند الکلهای سنگینتر) است و در نتیجه نیاز به خالصسازی دارد؛ این کار با تقطیر در برجهای تفکیک انجام شده و متانول با خلوص مورد نظر (معمولاً بالای ۹۹٪) به دست می آید.
واحدهای صنعتی تولید متانول و مقیاس تولید
فرآیند تولید صنعتی متانول طی دهههای اخیر به سمت مقیاسهای بزرگتر و بهرهوری بالاتر پیش رفته است. واحدهای مدرن متانول معمولاً ظرفیت تولید روزانه در حدود ۲۰۰۰ تا ۲۵۰۰ تن متانول را دارا هستند و فناوری طراحی واحدهایی با ظرفیت بالاتر (حتی تا ۵۰۰۰ تن در روز در یک واحد) نیز توسعه یافته است. فناوری تولید متانول (اعم از گاز طبیعی به متانول یا ذغال سنگ به متانول) توسط شرکتهای بین المللی متعددی ارائه میشود و این تعدد ارائهدهندگان فناوری نشاندهنده پختگی و قابلاطمینان بودن فرآیند متانول در مقیاس صنعتی است.
شایان ذکر است که در سالهای اخیر بخش عمدهای از طرحهای جدید تولید متانول در جهان با استفاده از ذغال سنگ به عنوان خوراک احداث شدهاند. برای مثال، تنها در فاصله سالهای ۲۰۱۱ تا ۲۰۱۴ میلادی حدود ۱۱ گیگاوات ظرفیت تولید گاز سنتز برای واحدهای متانول زغالسنگسوز در کشور چین راهاندازی شده است که بیانگر سرعت رشد بالای صنعت متانول مبتنی بر ذغال سنگ است. در حال حاضر فرآیند تولید متانول از گاز سنتز (با خوراکهای متنوع از جمله گاز طبیعی، ذغال سنگ, بیوماس یا پسماندهای هیدروکربنی) یک فناوری تثبیتشده محسوب می شود و در مقیاس جهانی دهها واحد صنعتی مشغول به تولید متانول هستند.
متانول صنعتی و کاربردهای آن
بخش عمده متانول تولیدی در دنیا برای تبدیل به سایر محصولات شیمیایی مصرف می شود. مهمترین مشتقات متانول عبارتند از فرمالدهید (برای تولید رزینها و پلاستیکها)، اسید استیک (برای تولید پلیمرهایی مانند پلیاتیلن ترفتالات و استاتها), متیل ترشیو-بوتیل اتر یا MTBE (افزودنی بنزین برای افزایش عدد اکتان) و متیل متاکریلات (برای تولید پلیمرهایی مانند پلیمتیل متاکریلات معروف به پلکسیگلاس). همچنین متانول در تولید سوختهایی نظیر دیمتیل اتر (DME) به عنوان جانشین گازوئیل و در فرآیندهایی مانند تبدیل متانول به الفینها (MTO) جهت تولید اتیلن و پروپیلن استفاده می شود. به دلیل خواص حلالیت خوب، متانول به عنوان حلال صنعتی نیز کاربرد دارد و در ضدیخها و شویندههای شیمیایی نیز به کار می رود.
متانول به عنوان سوخت جایگزین
متانول به عنوان سوخت پاک و جایگزین بنزین نیز مطرح است. ارزش حرارتی متانول تقریباً نصف بنزین است، اما عدد اکتان بالا و آلایندگی پایینی دارد. به دلیل نداشتن پیوندهای کربن-کربن در ساختار خود، احتراق متانول دود و دوده بسیار کمتری نسبت به بنزین تولید می کند و فاقد گوگرد است؛ لذا اکسیدهای گوگرد (SOx) در خروجی اگزوز ندارد. امروزه در برخی کشورها (مانند چین) متانول به صورت مخلوط ۱۵٪ در بنزین (M15) یا حتی خالص در خودروهای اختصاصی استفاده می شود. همچنین سالها در مسابقات اتومبیلرانی (IndyCar) از متانول خالص به عنوان سوخت استفاده شده است زیرا در صورت آتشسوزی به راحتی با آب خاموش می شود و خطر انفجار کمتری دارد.
در سالهای اخیر توجهها به متانول به عنوان سوخت کشتیها و ناوگان دریایی جلب شده است. متانول در دمای محیط مایع است و می توان آن را مشابه بنزین یا گازوئیل در مخازن معمولی سوخت ذخیره کرد، در حالی که سوختهایی مانند گاز طبیعی مایع (LNG) نیاز به مخازن برودتی پیچیده دارند. شرکتهای کشتیرانی پیشرو شروع به سرمایهگذاری در کشتیهای مجهز به موتورهای دوگانهسوز متانول کردهاند. متانول در مقایسه با نفت کوره سنگین که به طور سنتی در کشتیها مصرف می شد، آلایندگی بسیار کمتری از نظر اکسیدهای گوگرد (SOx) و ذرات معلق دارد و می تواند الزامات سختگیرانه استانداردهای آیمو (IMO) برای سوخت کشتی را برآورده کند. از متانول همچنین می توان در سلولهای سوختی (Fuel Cell) جهت تولید برق استفاده کرد یا آن را به سوختهای دیگری مانند بنزین (از طریق فرآیند MTG) یا دیمتیل اتر (جایگزین گازوئیل) تبدیل نمود.
مزایا، چالشها و ملاحظات زیستمحیطی
فرآیند تولید متانول از ذغال سنگ و هیدروکربن های سنگین دارای مزایا و معایب خاص خود است که در زیر به برخی از آنها اشاره میکنیم:
مزایا:
دسترسی به خوراک ارزان و فراوان: ذغال سنگ در بسیاری از کشورهای دنیا به مقدار زیاد و با قیمت پایین در دسترس است، و هیدروکربن های سنگین نظیر نفت کوره و پت کک نیز به عنوان محصولات جانبی پالایشگاهها فراواناند. این امر امکان تولید متانول را مستقل از منابع گاز طبیعی فراهم می کند.
امنیت انرژی و تنوعبخشی به سبد سوخت: با تبدیل ذغال سنگ و پسماندهای نفتی به متانول (سوخت مایع با آلایندگی پایین)، کشورها می توانند وابستگی خود به واردات نفت یا گاز را کاهش دهند و از منابع داخلی برای تامین سوخت جایگزین استفاده کنند.
کاهش آلایندههای محلی: گازسازی اجازه می دهد عناصر ناخالص مانند گوگرد و فلزات سنگین پیش از احتراق سوخت حذف و بازیابی شوند؛ متانول تولیدی نیز هنگام مصرف، سوختی پاکتر از نفت خام یا ذغال سنگ است (بدون سولفور و با تولید دوده کمتر)، ضمن اینکه گوگرد حذف شده نیز به شکل گوگرد عنصری قابل بازیابی است.
چالشها:
انتشار دیاکسید کربن و اثرات زیستمحیطی: تبدیل ذغال سنگ به متانول از نظر انتشار CO2 بسیار پُرکربن است؛ برای هر تن متانول تولیدی از ذغال سنگ، چندین تن CO2 تولید می شود که در صورت رهاسازی می تواند به تشدید تغییرات اقلیمی بیانجامد. اگرچه می توان CO2 حاصل را در فرایند جدا کرده و به صورت دائم ذخیره یا دفن نمود، اما این کار مستلزم هزینه قابل توجه و زیرساخت صنعتی پیشرفته است.
مصرف بالای انرژی و آب: گازسازی و واحدهای جانبی آن (مانند تولید اکسیژن و تصفیه گاز) انرژی زیادی مصرف می کنند. بازده تبدیل حرارتی ذغال سنگ به متانول پایینتر از فرآیندهای مبتنی بر گاز طبیعی است. همچنین فرآیند گازسازی نیاز به آب فراوان برای تولید بخار و خنکسازی دارد؛ به طوری که تخمین زده می شود تولید هر تن متانول از ذغال سنگ حدود ۲۰ مترمکعب آب نیاز دارد. مصرف بالای آب و تولید پساب می تواند به لحاظ زیستمحیطی در مناطقی با محدودیت منابع آب چالشبرانگیز باشد.
هزینه سرمایهگذاری و پیچیدگی عملیاتی: ساخت و راهاندازی واحدهای گازسازی ذغال سنگ یا خوراک های سنگین بسیار پرهزینهتر از واحدهای متانول مبتنی بر گاز طبیعی است. این واحدها به تجهیزات پیشرفتهای مانند راکتورهای گازساز فشار بالا، واحد تولید اکسیژن، سیستم های تصفیه گاز و دفع پسماند نیاز دارند که سرمایهگذاری اولیه سنگینی را می طلبد. همچنین بهرهبرداری ایمن و پایدار از چنین مجتمعهایی نیازمند دانش فنی و کنترل دقیق است.
ملاحظات ایمنی و سلامت: متانول مایعی سمی است؛ تماس مستقیم یا نوشیدن آن برای انسان خطرناک و حتی کشنده است. شعله متانول نیز کمرنگتر و دشوارتر قابل مشاهده است؛ بنابراین حمل و نقل و ذخیرهسازی آن باید با احتیاطات ویژه انجام شود.
نتیجهگیری
تولید متانول از ذغال سنگ و هیدروکربن های سنگین یک راهکار صنعتی اثباتشده است که امکان بهرهگیری از منابع کربنی فراوان و ارزان را برای تولید یکی از مواد پایه صنایع شیمیایی فراهم می کند. این فناوری به ویژه برای کشورهایی که دسترسی محدودی به گاز طبیعی دارند (مانند چین) اهمیت راهبردی داشته و به آنها اجازه داده است تا سوختها و محصولات شیمیایی ارزشمندی را از منابع داخلی خود تولید کنند. فرآیند تبدیل ذغال سنگ به متانول در مقیاس وسیع عملیاتی شده و در کنار مزایایی همچون امنیت انرژی و تولید سوخت پاکتر، با چالشهایی نظیر انتشار بالای CO2 و هزینه سرمایهگذاری زیاد مواجه است. با وجود این چالشها، این روش تولید همچنان در حال گسترش است و بخش عمدهای از تولید متانول جهان را تشکیل می دهد. از سوی دیگر، همزمان سرمایهگذاریها برای تولید متانول سبز (از منابع تجدیدپذیر یا بازیافت CO2) رو به افزایش است تا در آینده بتوان از مزایای متانول به عنوان سوخت و ماده خام صنعتی بدون آسیبهای زیستمحیطی بهرهمند شد. در مجموع، می توان گفت که تولید متانول از ذغال سنگ و هیدروکربن های سنگین پلی میان منابع فسیلی سنتی و نیازهای دنیای مدرن به سوختها و مواد اولیه صنعتی را فراهم کرده است و تا زمانی که انتقال کامل به منابع پاکتر میسر شود، نقشی کلیدی در صنایع انرژی و شیمیایی ایفا خواهد کرد.